In ongoing construction, project managers will need structural wood for concrete formwork. In urban and metro areas full of visually pleasing concrete buildings, they may be looking for formply that matches strength with high-quality. But what exactly is formply?
Formply is structural plywood primarily for formwork, holding and protecting concrete until it sets. Sheets have a laminated face that provides additional benefits not found in regular plywood. A hard, durable surface resin on both sides gives concrete builds a smooth finish. It has a hardwood core and often has a black overlay.
WHAT IS FORMPLY MADE OF?
Formply sheets incorporate a high-density overlay of impregnated paper bonded to a plywood core. Premium grade phenolic resin acts as a glue. As a result, formply a type-A marine bond, the strongest plywood bond available.
The bond gives the structural plywood enduring resistance against hot and cold. Performance is not affected if the sheet is partially submerged in water.
The plywood uses several thin sheets of wood glued together, similar to LVL Timber. The laminate and glue create resistance to cracking from nails, shrinking or warping. Figure 1 displays formply sheets and their layers.
Sheets are available in multiple sizes. However, 2400x1200mm and 1800x1200mm remain the most popular. Sheets come in 12, 17, 19, and 25mm thicknesses.
There are a variety of sheets with different cores on the market including birch, eucalypt and radiata pine. Construction personnel have the option to choose between these cores to suit their specific needs.
DIFFERENCE BETWEEN F14 AND F17 PLYWOOD?
Formply receives stress grades from F11 to F27, depending on strength. The most commonly available on the market are the F14 and F17 varieties. Deciding between the two depends on the budget and structure of the building.
As the value suggests, F14 formply can withstand 14 megapascals (MPa) of pressure, whereas F17 can withstand 17 MPa. For more demanding builds, F17 is the winner for its superior ability for load-bearing.
F17 is the sheet of choice for many, but there are even stronger sheets if necessary as shown in Figure 2 below.
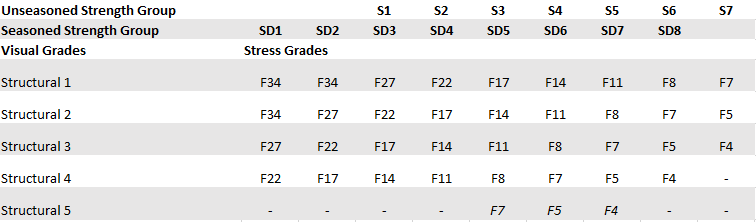
Figure 2: F stress grading via Australian Standard 2878
MARINE VS REGULAR PLYWOOD
Not all structural plywood is labelled as marine due to the strict criteria it must fulfil.
Voids cannot be present in the inner veneer layers due to their delaminating effect. The risk of it occurring rises when there is a build-up of moisture. Manufacturing must also use waterproof glue.
Finally, marine plywood requires a higher grade face veneer than what is on exterior grade plywood.
FORMPLY VS MARINE PLYWOOD
Workers would coat marine plywood sheets in oil for a smooth finish before formply. F17 expands upon marine plywood, ideal for use in areas of constant contact with moisture.
The outer face is waterproof, allowing for easy separation from curing concrete. Formply is attractive with a variety of colour available for home furnishing.
Formply exceeds marine plywood despite not technically meeting its criteria.
IS FORMPLY WATERPROOF?
Formply is water-resistant but not entirely waterproof. Sheets are designed to withstand moisture on-site through their high-density overlay.
The film on top is waterproof, while the edges are sealed to ensure no moisture is absorbed. Concreters can re-use sheets on many sites thanks to quality materials and manufacturing
FORMPLY APPLICATIONS
Formply combines features of architectural and structural plywood to create a strong and modern product. Its primary use is in concrete formwork. The panels hold the concrete in a mould until it sets.
F17 use is widespread on beams, bridges, large deck forms, and other civil engineering projects. It has even been used to build a python enclosure! Figure 3 demonstrates formply uses for construction and interior spaces.
A frequent question we receive is whether you can paint on formply. AUSF advise against doing this for anyone considering. Any paint that finds its way onto the film surface will fall off, similarly to how sheets detach from set concrete.
ADVANTAGES OF FORMPLY
Formply satisfies Australian Standard (AS) 6669 which classifies as high performing plywood. The standard ensures panels are acceptable to use in load-bearing operations.
Another benefit is customisation. Consumers can order in different colours for interior spaces and not visually degrade them.
Furthermore, the additional laminated sheet offers moisture protection. Although not waterproof like marine plywood, it is still the favourite for high moisture areas.
The phenolic resin provides protection in all weather and prevents expansion and warping. Sheets can also cope with UV and saltwater.
While complying with AS 6669 due to its strength, formply is popular for its durability. The film surface protects the front and back from damage. The core itself is protected from damage by the laminated layer. As a result, formply is an extremely durable plywood that is versatile and re-useable.
It can be daunting and we do encourage you to research what you need for the job at hand. 2400 x 1200mm and 1800 x 1200mm F17 Formply that is ideal in indoor and outdoor spaces.