1 RAW MATERIAL
We use material from rubber wood only, making our board homogeneous, high quality and environmental, friendly.

2 CHIPPING AND FLAKING
Rubber wood were chipped before reduce to desired fine flakes. The control of flake sizes is the heart of optimum strength and smooth surface.

3 DRYING AND SCREENING
The wet falke are dried to the controlled moisture level after dried, the flakes are screened to separate for the core layer and the surface layer.

4 GLUE MIXING & BENDING
The particles for core and surface are mixed with glue, wax emulsion and additive substance to achive the desired quality.

5 MAT FORMING
The mixed particles are spread by computer control equipment, to ensure the consistency and uniform of the board property.

6 HOT PRESS
Hot press shall compress the mat of particles under high pressure and temperature to form the precise board thickness and quality.
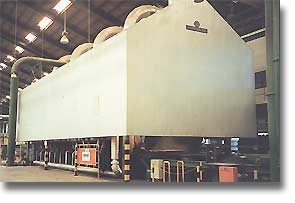
7 COOLING
After pressed the board shall be cooled to ensure the glue setting.

8 CUT TO SIZE
sizes 3′ x 6′, 4′ x 8′, 4′ x 6′ are the main sizes, besides we are able to supply the customized cutting.

9 SANDING
The raw particle board are sanded to fine surface.
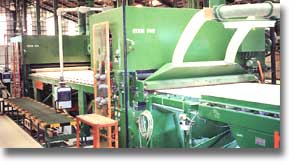
10 GRADING
All board were graded to ensure high quality of board.

11 PACKING AND DELIVERY
Packing as our standard delivery can be made by truck of vessel